Developing VLE and LLE Equilibrium Studies
The first step of pilot plant testing typically involves acquiring vapor-liquid equilibrium (VLE) or liquid-liquid equilibrium (LLE) data. Accurate VLE and LLE data are essential for the design of mass transfer processes, but are not always available in literature. That’s why it must be developed prior to the design phase. Koch Modular employs experienced process engineers who can design cost-effective test programs, interpret experimental data, and use pilot plant testing techniques to confirm a design.
Flexible, State-of-the-Art Pilot Plant Facility
With more than 5,000 square feet of floor space and 32 feet of headroom, our facility is well-equipped to facilitate both bench- and pilot-scale tests. Our ability to modify column internals and auxiliary equipment gives us the flexibility to test different configurations and quickly arrive at an optimum solution. Our in-house analytical department supports all pilot tests, providing customers with on-the-spot feedback to significantly reduce time spent in the pilot plant.
Pilot tests are performed over a range of operating conditions to measure mass transfer efficiency and determine optimum conditions. Sufficient data for scale-up is routinely generated within one week of testing for each process step. With years of experience, Koch Modular has developed proven correlations that provide accurate scale-up from pilot to commercialization.
Access to Full-Scale Separation Equipment
The final product of the pilot plant test is a test report that guides Koch Modular on designing and supplying the complete commercial-scale separation equipment. With the pilot testing completed and the scale-up factors determined, Koch Modular can provide mass transfer separation equipment such as a Distillation Modular System or a Liquid-Liquid Extraction Column with a Process Performance Guarantee.
Why Use a Pilot Plant with Koch Modular?
Our pilot plant is used to develop vapor-liquid and liquid-liquid equilibrium data and study these processes. Accurate VLE and LLE data are key elements of most mass transfer processes. These sets of data, however, are not available in literature and must be developed before a design can be created. Below are more reasons on why Koch Modular’s pilot plant can meet your needs:
Full Range of Pilot Testing Services
- Feasibility Studies
- VLE/LLE Development
- Process Design
- Pilot Plant Testing
Extensive Process Experience
Unrivaled Analytical Capabilities
- Chromatography
- Spectrophotometry
- Wet Chemistry
- Karl Fischer
Unit Operations Offered at Our Pilot Plant
Distillation Testing Services
Distillation Capabilities
Column Configurations
- Packed, Trays, Multiple Feeds, and Sidedraw.
- Column diameter between 1″ and 4″; up to 60 theoretical stages.
Operating Pressures
- Pressure to 30 PSIG.
- Vacuum to 1 mmHG.
Reboiler Types
- Kettle, Thermosiphon, Forced Circulation, and Falling Film.
Heat Sources
- Steam, Hot Oil, and Electric
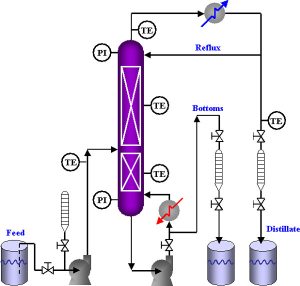
Every distillation pilot plant test involves a customized setup for each industrial application. Varying configurations are available for flashing, steam stripping, vacuum, azeotropic, multi-component and non-ideal processes. The pilot column is run over a range of operating conditions to measure separation performance and help determine the optimum operating conditions. Observations, such as operating stability, foaming, fouling, or thermal degradation, are also important for process scale-up. Some of our distillation capabilities are outlined below.
Liquid-Liquid Extraction Tests
Extraction Capabilities
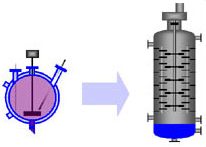
In a number of applications, liquid-liquid extraction must be tested at elevated pressure due to the temperature and the vapor pressure of the material handled. Koch Modular has available for rental a 1″ diameter KARR® Column and 3″ diameter SCHEIBEL® Column, both in 316SS construction. These columns can be sent to the clients facility for on-site testing, along with operating and engineering personnel.
Customized Steam Stripping Setups Available at Pilot Plant
Steam stripping is a multistage distillation process in which steam is used as a stripping gas to remove hydrocarbons from wastewater. It is commonly used as a cost-effective mass transfer technique to meet EPA regulations. Many organic contaminants can be easily stripped from an aqueous stream. Because it is concentrated in the rectification section of the column, the amount sent to disposal is significantly reduced.
Pilot testing allows Koch Modular to understand the steam stripping application and its individual process characteristics (foaming tendency, fouling propensity, impact of ‘bad players’ and overall operating stability) by processing drum quantities of ‘actual’ wastewater, developed in our customers’ processes. Pilot plant equipment setups are customized to each client’s unique applications. Koch Modular has successfully removed compounds including alcohols, ketones, aromatics, aliphatics, acetates, and chlorinated hydrocarbons.
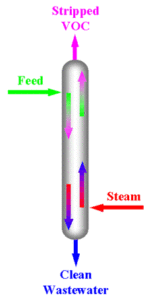
Below is a partial list of compounds that Koch Modular has successfully removed with steam strippers:
Alcohols | |||||||||
---|---|---|---|---|---|---|---|---|---|
Methanol | Ethanol | Propanols | Butanols | Amyl Alcohol | |||||
Ketones | |||||||||
MEK | Acetone | MIBK | |||||||
Aromatics | |||||||||
Benzene | Toluene | Styrene | Xylenes | Alkylbenzenes | Naphthalene | Methyl Naphthalene | Naphthalenes | ||
Aliphatics | |||||||||
Hexane | Heptane | Cyclohexane | |||||||
Acetates | |||||||||
Methyl Acetate | Ethyl Acetate | Propyl Acetates | Butyl Acetates | Amyl Acetate | |||||
Chlorinated Hydrocarbons | |||||||||
Methyl Chloride (dichloromethane) | Chloroform | Carbon Tetrachloride | Ethylene Dichloride | TCE’s | |||||
Others | |||||||||
Acetaldehyde | Acetonitrile | Ammonia | Dioxane | Formaldehyde | H2S | HCN | Isopropyl Ether | TEA | THF |
Pilot Testing a Reaction Process is Vital for Plant Design
Pilot testing a reaction is often a vital part of developing a commercial scale plant design. Koch Modular has experience in the following types of reaction studies:
- Homogeneous Batch/Semi-Batch Reactions
- Homogeneous Continuous Reactions (Plug Flow)
- Reactive Distillation – Homogeneous
- Reactive Distillation – Heterogeneous
Homogeneous Batch / Semi-batch Reactions
These are the most common reaction types and often require constant removal of a product via distillation and distillation testing for the reaction to progress.
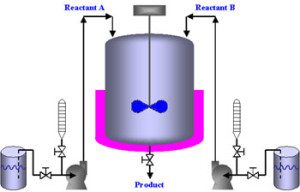
Homogenous Continuous Reactions (Plug Flow)
This style is useful for fast reactions where high throughput is essential. Reactors can range from piping loops to agitated extraction columns such as SCHEIBEL® or KARR®. In one application, a KARR® column replaced a series of Continuous Stirred Tank Reactors (CSTRs) and provided higher yield and purity.
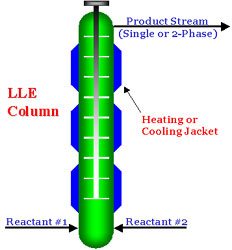
Reactive Distillation – Homogeneous
Homogeneous reactive distillations combine mixing and heat transfer inside a distillation column. Two-unit operations, reaction and distillation are performed in the same piece of equipment to achieve greater cost savings.
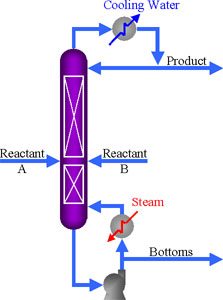
Reactive Distillation – Heterogeneous
Heterogeneous reactive distillations are performed in distillation columns that have three sections. The reactor section is in the middle, with a rectifying section above and a stripping section below. To achieve greater cost savings, two-unit operations, reaction and distillation are performed in the same piece of equipment
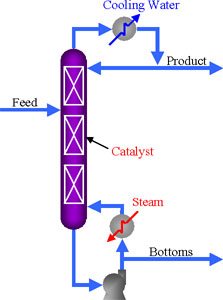
Miscellaneous Applications
Koch Modular can evaluate and test a number of unit operations for separation processes. In addition, these unit operations are typically evaluated for processes that include LLE or distillation steps. Koch Modular can also work with clients on a one-on-one basis for these types of processes.
Other types of processes we evaluate in our pilot plant include:
- Crystallization
- Heat Transfer Coefficient Studies
- Thin Film Evaporation (partnership with LCI Corporation)
- Absorption
- Coalescing
- Ion Exchange Beds
- Carbon Adsorption
- Filtration
- Membrane Separations
Koch Modular LLE columns have also been applied to a number of unique applications that can be tested in our pilot plant.
Single Stage Mixer / Settler
Both the KARR® and SCHEIBEL® columns can be used as co-current, mixer/settlers. The typical mixer/settle used industrially will only generate up to 85% of a theoretical stage due to back mixing inefficiencies. However, the co-current KARR® or SCHEIBEL® Column can achieve essentially 100% of a theoretical stage at extremely high capacity if it is operated in plug-flow mode.
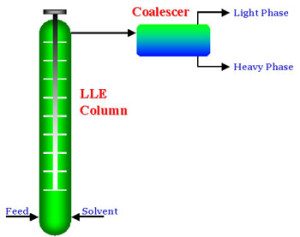
Slurry Processing
Koch Modular has demonstrated that the KARR® Column can effectively handle slurries with up to 50% solid’s concentration. The perforated plates with 55-60% open area allow solids to flow through without accumulating. Slurry feed must have solids that sink through the up-flowing solvent and accumulate in the bottom chamber of the column. The agitation provides the means for maximizing solid-to-liquid mass transfer.
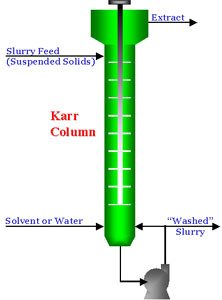
Pilot Plant Examples of Modular Process Projects
The primary goal for most tests performed in the Koch Modular Pilot Plant is to generate the data required for successful scale-up to production equipment. Scale-up from Pilot Plant data forms the basis of our process performance guarantees. In this section, we will cover a number of recent applications where testing led to the design and implementation of production equipment. These pilot testing columns include fragrance fractionation, product recovery through fractionation, solvent recovery and other extraction techniques for mass transfers.
Pilot Plant Testing for Citrus Oil Fractionation
Koch Modular has successfully fractionated orange oil and other citrus oils to produce many commercially desirable components. Pilot tests have included batch and continuous folding and fractionation steps to recover compounds such as octanal, pinene, limonene, linalool, citronella, dodecanal, valencene, and nootkatone. These tests typically require high vacuum to limit the operating temperature.

Pilot Plant Testing of Fractional Extraction for Product Recovery
Koch Modular successfully tested a fractional extraction application involving a light “tar” feed stream from a refinery operation using a SCHEIBEL® Column. For this application, the organic feed was added in the middle zone of the column. A polar solvent was added at the top of the column to preferentially extract more polar, aromatic components (product stream). A straight-chain hydrocarbon was added at the bottom of the column and preferentially extracted the non-polar organics (impurities). The test program successfully demonstrated over 92% product recovery with less than 1% impurities. A production column was designed, built, installed and deployed with excellent product recovery and purity achieved.
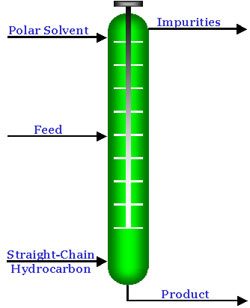
Pilot Plant Testing for Biodiesel Distillation
Koch Modular has successfully recovered Biodiesel (methyl esters) from a crude Biodiesel feed stream. The process was piloted in three steps. The first step was an evaporation step that removed methanol and lights. The second step involved the removal of excess glycerin. The last step collects the Biodiesel as a distillate product. All three steps are performed under a vacuum. A commercial system was designed, built and deployed by Koch Modular. The modular system is currently in operation.
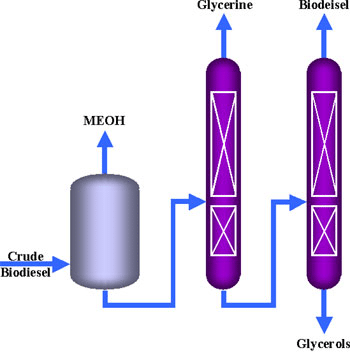
Pilot Testing a Replacement for a Poorly Performing Extraction Column
Koch Modular successfully tested the extraction of organic components including nitrated organics from an aqueous feed stream using an aromatic, organic solvent. Prior to testing, the client was using an antiquated RDC column in their production process, which left a high level of nitrated organics in the aqueous effluent. Testing in a SCHEIBEL® Column demonstrated higher extraction efficiency (lower nitrated organic level in the aqueous effluent) at a reduced solvent to feed ratio. Testing also demonstrated that changing the continuous phase resulted in significantly improved process hydraulic behavior (minimized emulsion formation and entrainment losses). A production column has been designed, built, installed, and successfully started-up.
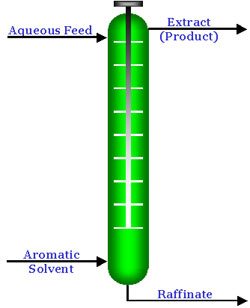
Pilot Testing Partially Water-Soluble Solvent Recovery and Drying
Koch Modular has successfully recovered a high-boiling partially water-soluble solvent from both phases of a decanted product. This was done in a multi-step process, but we processed both phases individually. After a wet solvent-rich stream was recovered, the water was stripped out. A commercial system was designed, built and deployed by Koch Modular. The modular system is currently in operation.
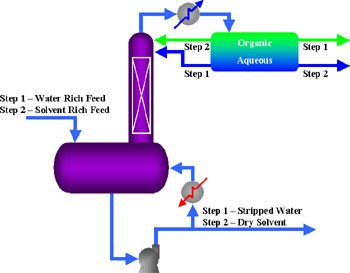
Pilot Test for Extracting Salts from an Organic Feed Stream
Koch Modular successfully tested the extraction of inorganic, chloride,and salts from a chlorinated organic feed stream; we used water as the solvent. A KARR® Column with PTFE perforated plates was tested for this application. The tests demonstrated that over 99% removal of the inorganic salts can be achieved for solvent to feed ratios as low as 0.07 (i.e., 0.07 weight of water to 1.0 weight of organic feed).
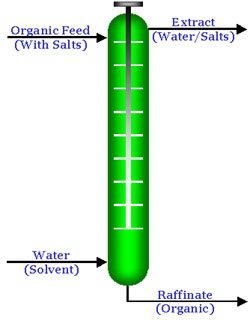
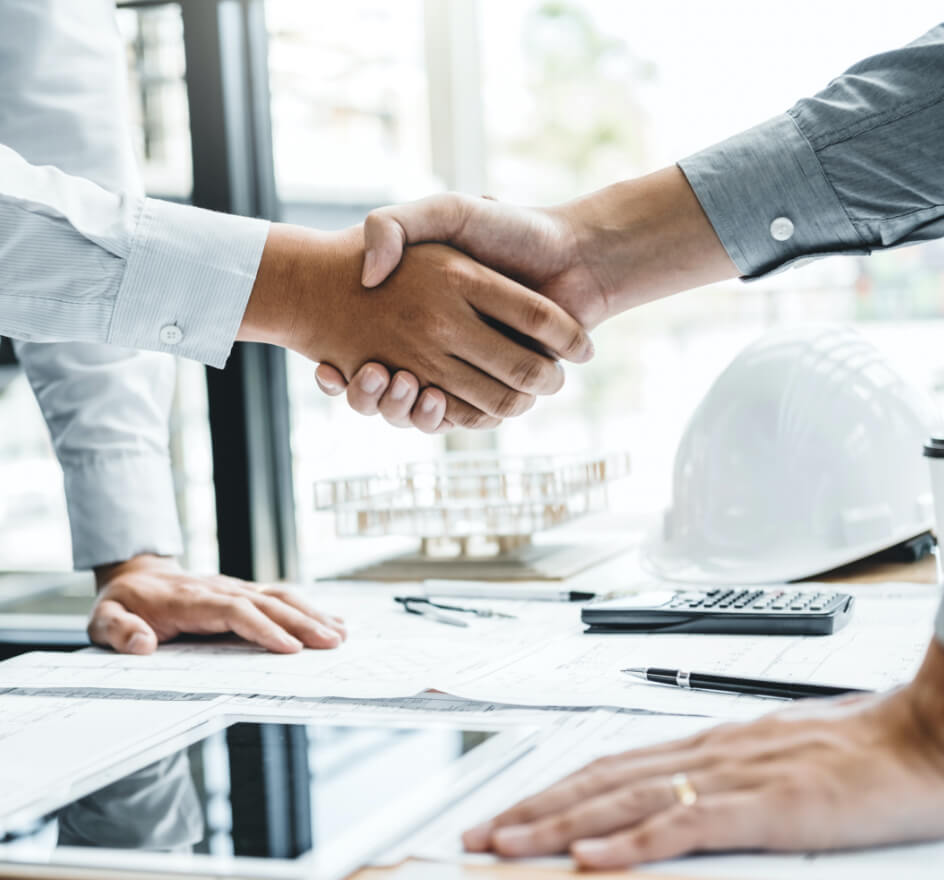
Pilot Plant Full Analytical Capabilities
The analytical department provides on-site analysis of process streams to assist with pilot/laboratory testing. Rapid analytical results are available to help direct the tests so that results can be obtained in the shortest time possible. Our analytical chemist is dedicated to supporting the pilot plant activities, and we always welcome input from the client’s analytical staff to assist in these tests.
The pilot plant testing team at Koch Modular Process Systems is fully capable of providing analytical support for the following equipment systems:
- GC
- HPLC
- Karl Fisher
- Wet Chemistry
- APHA Color
- Physical Testing
- Moisture Analyzer (balance)
- Surface Tensions
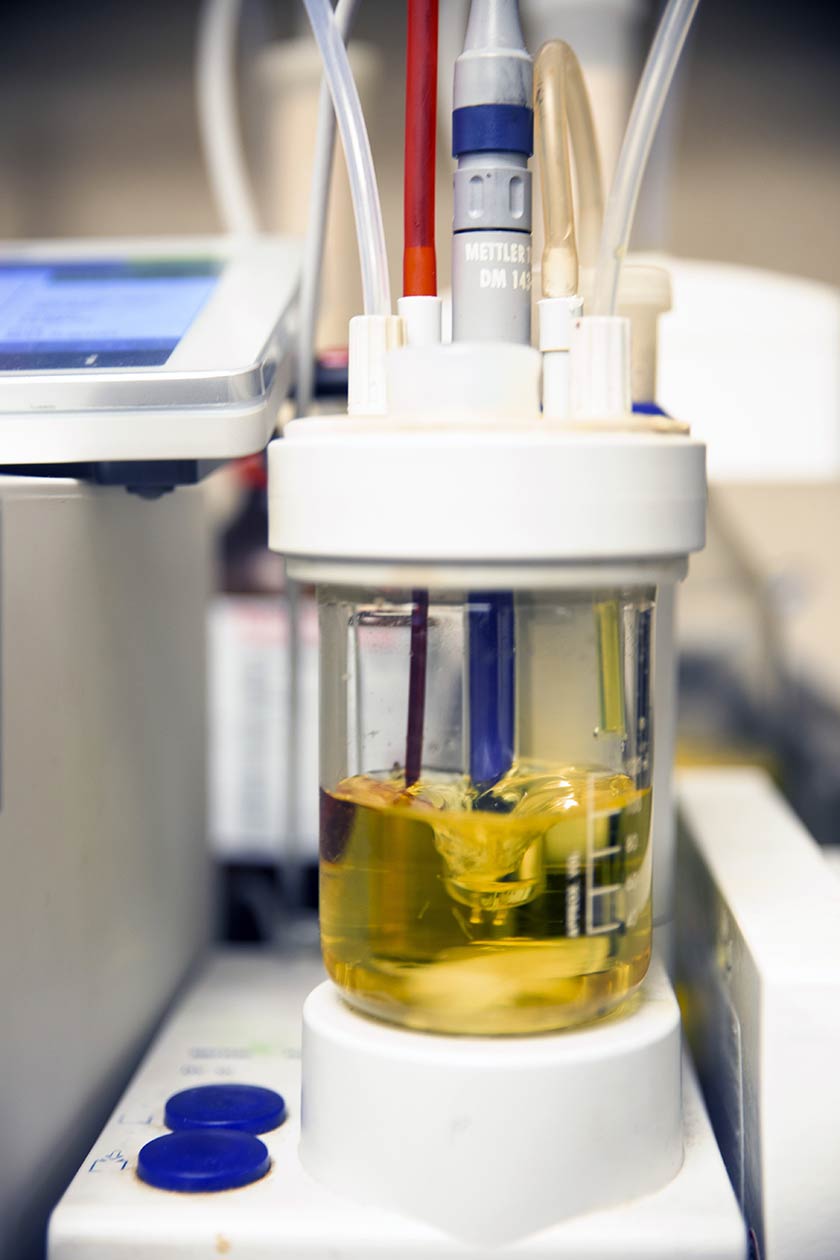
VLE and LLE Equilibrium Studies via Pilot Plant Testing
The first step in the process of pilot plant testing is often the development of vapor-liquid equilibrium or liquid-liquid equilibrium data.
Due to the non-ideal nature of many of the systems encountered, experimental equilibrium data is required for design. If this data is not found in the literature, it must be measured in the laboratory. Thus, it is often necessary to perform bench scale tests to fill gaps in the available data. LLE data for extraction and VLE data for distillation can be developed in our pilot facility.
Also important during LLE and VLE tests are observations by Koch Modular’s trained experts. For example, observations such as foaming or fouling often prove to be extremely valuable in avoiding potential operating problems in the pilot plant and/or commercial equipment.
This test data is incorporated into computer models to optimize the process and establish operating conditions for the pilot plant tests to follow.
Vapor-Liquid Equilibrium Development Study
- Presence of azeotropes
- Deviations from ideal behavior
Observations
- Foaming tendency
- Fouling tendency
- Degradation or thermal stability
- Solids precipitation
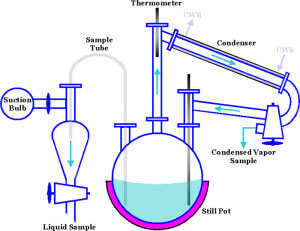
Liquid-Liquid Equilibrium Development Study
- Distribution Coefficient vs Solute Concentration
- Temperature and pH effects
Observations
- Separation time
- Emulsion formation tendency
- Interface behavior
- Rag layer formation
- Emulsion band formation
- Entrainment tendency in both phases
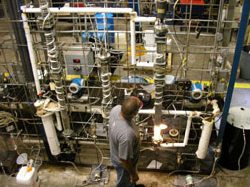