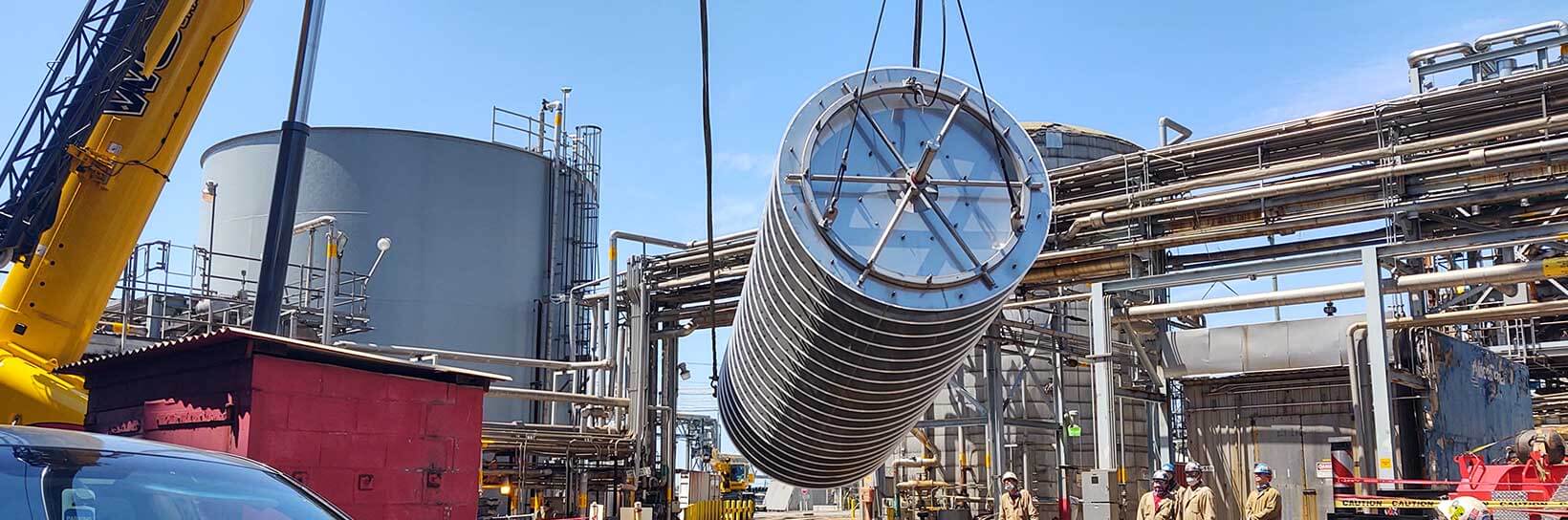
Koch Modular goes beyond designing and constructing liquid-liquid extraction columns. We continue the relationship with our customers after installation and startup. Koch Modular provides replacement parts, repair services, and troubleshooting assistance for all types of extraction columns. Our team consists of professional, skilled, and highly qualified technicians and engineers who can provide on-site mechanical and process-related support.
Reasons to Use Liquid-Liquid Extraction / Solvent Extraction
-
Recovery of water soluble components from immiscible organic streams
-
A complex distillation sequence is required
-
Processing of azeotropic and close boiling components
-
The component of interest is prone to thermal degradation or is non-volatile
-
Energy requirements of distillation are prohibitive
The general rule: LLE / SX can be avoided if it is more economical to separate chemicals of interest via distillation. However, there are other situations where liquid-liquid extraction / solvent extraction should be considered.
It is important to consider the solvent recovery aspects early in the development process since they can affect the overall project economics. In the example LLE / SX process below, approximately 3% of the operating cost is incurred in the extractor and the remaining 97% in solvent recovery. An extraction column followed by two distillation columns is a common way to design a system that recovers solvent and produces purified solute. In most cases, a majority of the capital cost is incurred downstream of the extraction column.
Koch Modular demonstrate how one of its patented KARR® Column Designs functions for liquid-liquid extraction.
Koch Modular has a variety of different extractors to choose from for various industrial applications. In this video, the KARRⓇ Column that is demonstrated is a form of agitated extraction. It has solid efficiency, turndown capability, uniform shear mixing, and is best suited for systems that emulsify. At Koch Modular, we don’t just sell extraction equipment; we supply solutions to your difficult separation applications.
Industry Applications
- Recovery of carboxylic acids from biomass such as fermentation broths
- Recovery of oil from algae broths
- Recovery of acetic acid from dilute solutions
- Washing of acids/bases, polar compounds from organics
- Recovery of acrylic acid
- Removal and recovery of phenol, DMF, DMAC
- Removal of nitrated organics
- Decaffeination of coffee and tea
- Separation of essential oils (flavors and fragrances)
- Purification of phosphoric acid
- Recovery of boron and bromine
- Recovery of cobalt, copper, manganese and nickel
- Recovery of rare earth elements
- Recovery/purification of alkali metal
- Purification of uranium
- Recovery of active materials from fermentation broths
- Purification of vitamin products
- Separation of olefins / paraffins
- Separation of structural isomers
- Lube oil quality improvement
- Separation of aromatics/aliphatics (BTX)
- Recovery of caprolactam for nylon manufacturing
- Separation of catalyst from reaction products
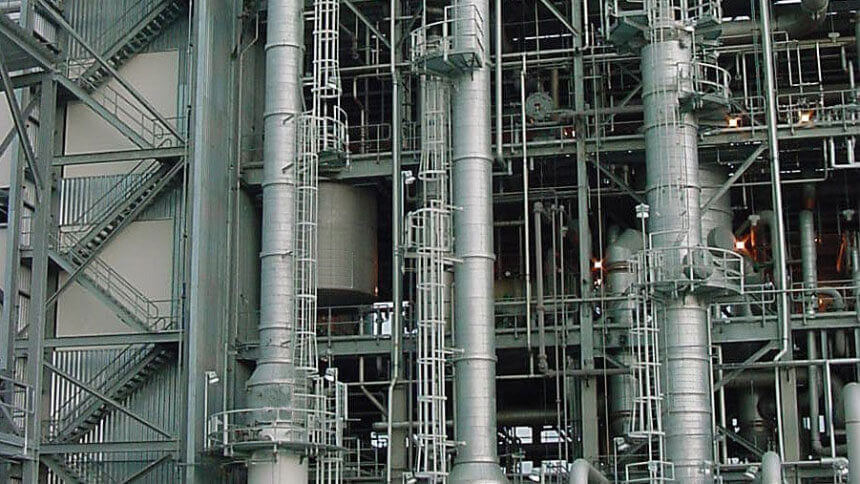
Complete System Design
In addition to the extraction column, the downstream distillation column design is also an important aspect of any extraction application that recycles and/or recovers solvents. At Koch Modular, we often supply extraction and distillation columns as a complete and integrated modular system for Solvent Recovery applications. Typical examples are illustrated on this page. From conceptualization through start-up, our professional and skilled engineers can provide sound guidance at every step of the liquid-liquid extraction process.
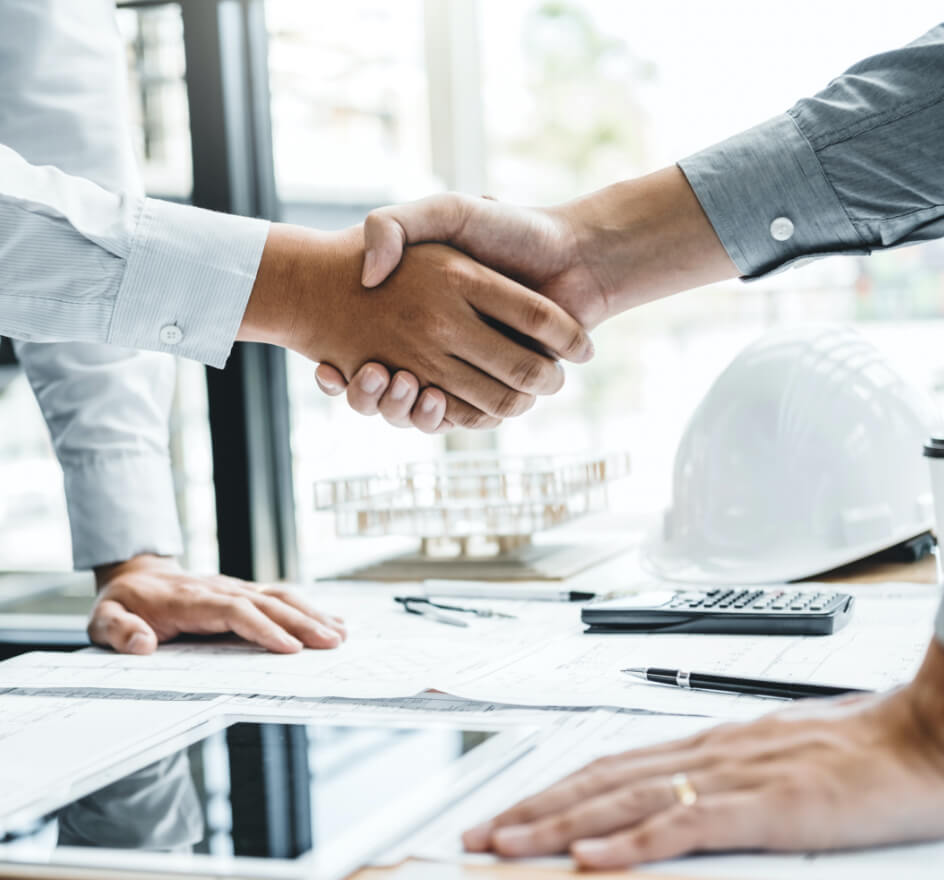
For over 40 years, Koch Modular has successfully designed and constructed mass transfer systems for the worldwide Chemical Processing Industry. Our customers rely upon us for our quality products and technical expertise.
Advantages of Modular Construction for LLE
- Weather conditions do not affect work progress
- Single source responsibility
- Prevent plant site safety concerns as construction is done offsite
- Construction of modular system can proceed while permits are still pending
- Minimal plant site interruption
- Compressed schedule
- Lower initial lump sum bids and operational costs
Introduction to Liquid-Liquid Extraction: Learn all about LLE. From theory, uses, industrial applications, design considerations and extraction equipment types.
For case studies by Koch Modular, check out our White Papers and Presentations.
Process Development: Laboratory Testing to Pilot Testing to Commercialization
Nearly all extraction projects require pilot testing to provide the basis for commercial process design and a process performance guarantee. Unlike distillation processes, which can often be designed using process simulation and hydraulic rating software alone, extraction involves complex chemical phenomena at the liquid-liquid interface which is very difficult to model to allow for commercial scale process design. Dispersed phase entrainment, emulsification tendency and the impact of impurities at the liquid-liquid interface are some of the common phenomena that occur in an extraction column which makes pilot testing essential. When conducting an extraction pilot test, it is highly preferable to use actual plant feed and solvent materials.
Before pilot testing begins bench scale tests are performed to generate liquid-liquid equilibrium data. In addition to supplying the equilibrium data, these tests can reveal phase behavior near the liquid-liquid interface such as emulsification or entrainment that help guide extractor selection.
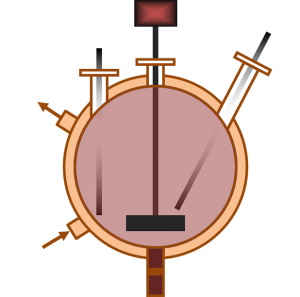
Why Pilot Testing
The best and most reliable method for the design of an LLE column is by pilot plant testing with actual feed and then using established scale-up correlations for the specific type of extraction technology.In general, the development procedure consists of the following steps;
- Selecting the solvent and generating liquid-liquid equilibrium data
- Using this information and the project requirements to select the column type to test
- Performing a pilot plant test to generate the data for accurate scale-up to the production column
- Designing and fabricating the column
Koch Modular designs pilot tests using a step-by-step optimization method. This allows the pilot test to save time and material. This method requires some experience but when applied correctly, will minimize the amount of feed and solvent used, and ensure that the commercial scale extraction column is designed correctly and performs as required.
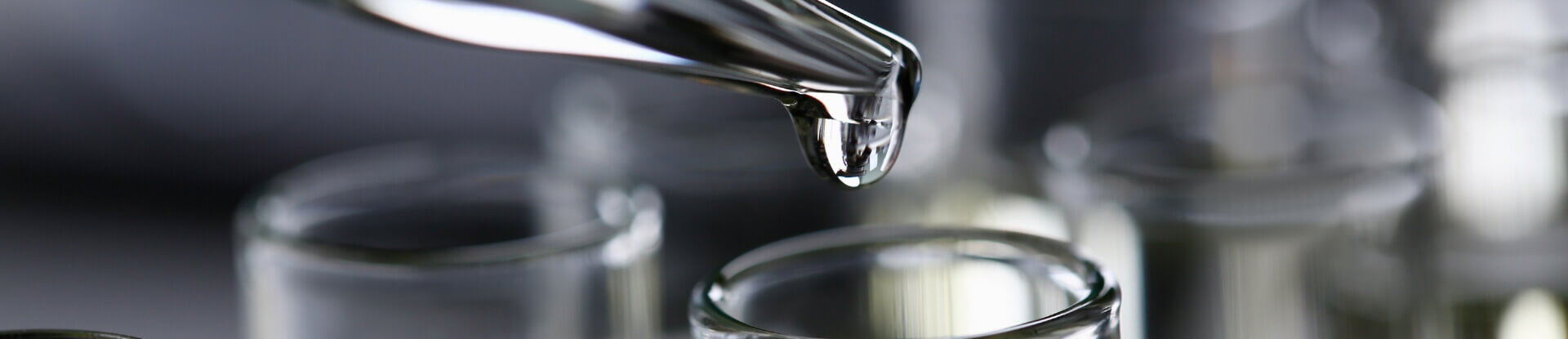
Bench Scale Tests Provide
-
Selection of extraction technology for pilot test
-
Settling times
-
Mixing characteristics
-
Equilibrium data
Pilot Scale Tests Provide
-
Development of basis for performance guarantee for commercial scale system
-
Optimization of liquid-liquid extraction separation
-
Complete process demonstrations
-
Useful data for scale-up projects (agitation speed, throughput, amd stage efficiency)
Liquid-Liquid Extraction Column: Selection, Scale-up and Design
The extraction column’s separation performance is measured during the pilot plant test. It is typically determined over an array of agitation speeds, effective heights, solvent-to-feed ratios, and capacities. Data from successful pilot testing results is used with proven scale-up equations and correlations to design an economical, commercial scale extraction solemn with an optimal set of operating conditions.
Koch Modular has a wide range of LLE / SX column technologies to choose from, both static and agitated columns. Click on the column types below for more information on each.
Our team of experienced engineers is available to work together with you on your next liquid-liquid extraction application, from conceptualization through start-up.