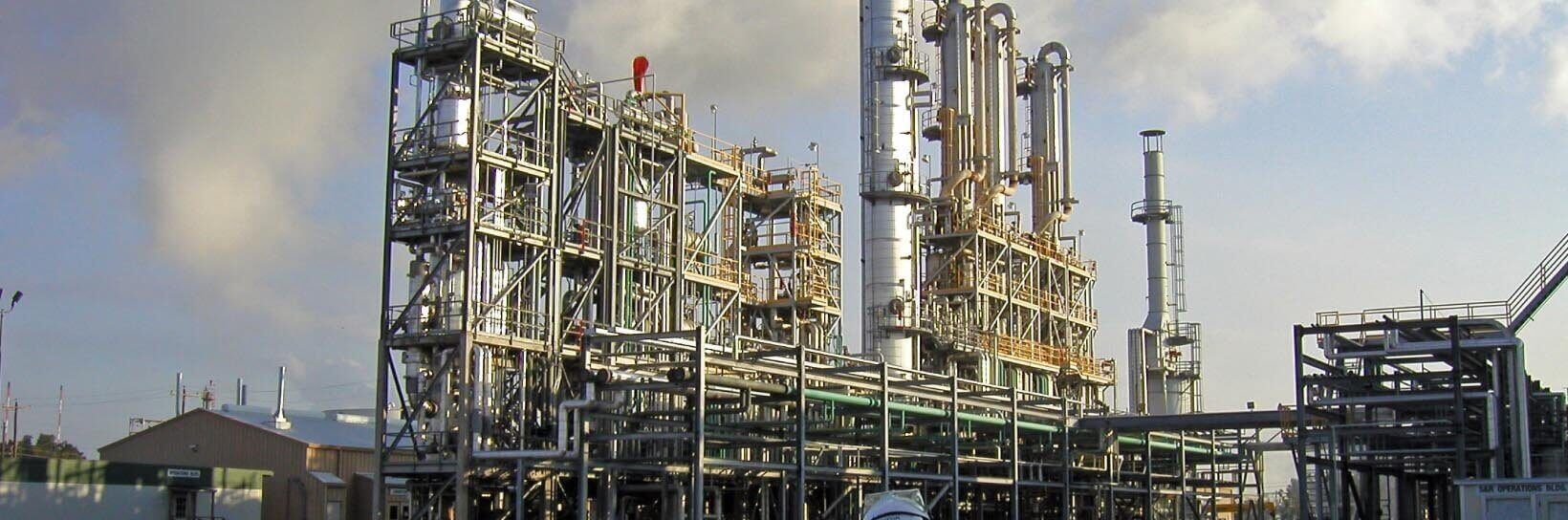
What is Steam Stripping?
Steam stripping, also known as steam distillation, is an affordable, one-step solution to cleaning volatile organic compounds (VOC) from plant wastewater streams. Typically, wastewater feed streams enter a distillation column at the top and flow downward, while steam enters the column at the bottom and rises. Pressure/temperature phase differences between the steam and contaminants allow the steam to strip the contaminants from the water. Based on applications, variables include methods to increase the water-steam surface contact area, pressures, temperatures, and others. It’s important to note that these processes must also meet the latest PEG (Pharmaceutical Effluent Guidelines), Environmental Protection Agency (EPA), and NESHAP regulations, including Miscellaneous Organic NESHAP (MON), Hazardous Organic NESHAP (HON), and Maximum Achievable Control Technology (MACT). Koch Modular is proud to offer design outcomes with unmatched adherence to all regulatory requirements.
Process design parameters depend on the particular VOCs present, concentrations, boiling points, and solubility, among other factors. Stripping is straightforward if the contaminants’ boiling points are lower than that of water, but different feedwater compositions may require additional design features. As a result, analysis and testing of design concepts is a critical step in system project planning, an integral element in Koch’s design process. Once extracted, the organic contaminants are removed from the system in a concentrated distillate stream. Minimizing this distillate stream’s volume is important to minimize the plant disposal costs.
Waste minimization is achieved by providing greater separation between the water and organic phases. This is accomplished by first condensing and then decanting the column’s overhead product to separate the water phase and the insoluble organic phase, with subsequent refluxing of the water phase from the decanter to the top of the stripping column. It is common to run the steam stripping process through several rectification stages and/or add reflux to the steam stripping column when stripped organics are soluble in water. This also helps reduce the water content of the organic contaminant distillate stream. The organic contaminants can then be drawn off as a liquid product for recycling purposes or disposal or as a vapor product fed to a thermal oxidizer.
Understanding Steam Stripping
Steam used to strip organic compounds is injected at the bottom of a steam stripping column. Wastewater is injected at the top of the column. The steam rises in the column and flows upward, countercurrent to the water. Often packing, trays or other materials are placed in the column to increase the surface contact between the steam and water, resulting in greater contaminant removal. The steam containing the organics is collected at the top of the stripping column, condensed, and separated via a decanter. The condensed steam is then refluxed to the top of the stripper column. Koch design engineers stay up-to-date with and incorporate all applicable EPA, environmental, state, or local regulations into any design. Client requirements and general procedural, health, safety, and other essential project-related conditions are part of every Koch project. All systems meet Maximum Achievable Control Technology (MACT) standards set by the EPA.
Koch Modular Process Systems is the leader in modular process system construction, saving our customers both time and money. Components of the final system are constructed as modules at our module construction shop, under the roof, which means work continues regardless of the weather. This approach is safer, and construction can be conducted in parallel with securing required permits. This means our customers save months from project initiation to implementation. Learn more about the benefits of modular construction here.
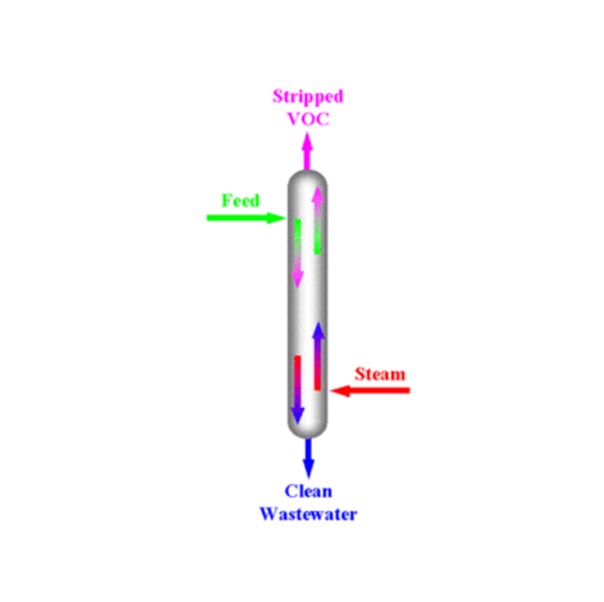
Steam Stripper Applications
Steam stripping, also known as steam distillation, is an economic method of cleaning up plant wastewater streams. It is a multistage continuous distillation process where steam is used as a stripping gas to remove hydrocarbons from dischargeable waste waters; while meeting the latest EPA, PEG (Pharmaceutical Effluent Guidelines) and NESHAP regulations such as MACT, HON, and MON.
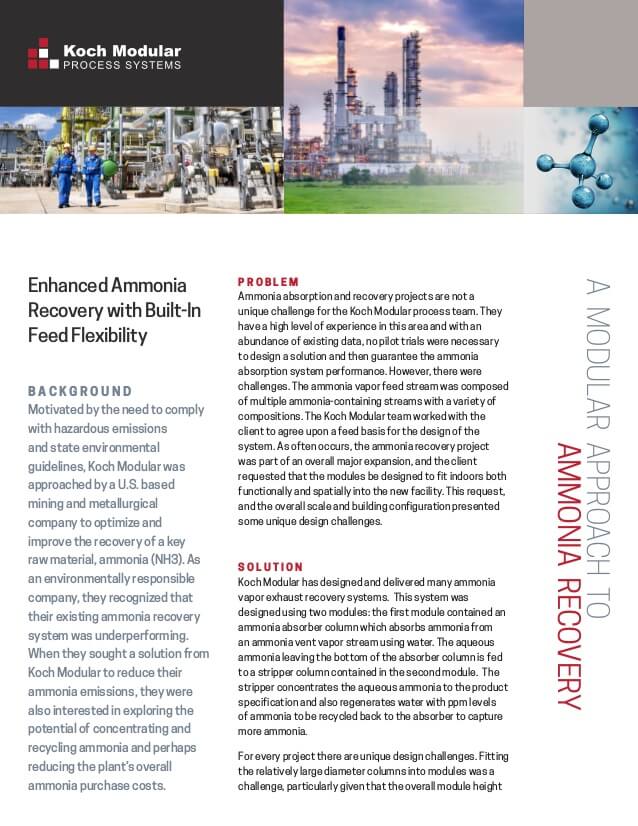
Ammonia Recovery
Ammonia absorption and recovery projects are not a unique challenge for the Koch Modular process team. They have a high level of experience in this area and with an abundance of existing data, no pilot trials were necessary to design a solution and then guarantee the ammonia absorption system performance. However, there were challenges. The ammonia vapor feed stream was composed of multiple ammonia-containing streams with a variety of compositions. The Koch Modular team worked with the client to agree upon a feed basis for the design of the system. As often occurs, the ammonia recovery project was part of an overall major expansion, and the client requested that the modules be designed to fit indoors both functionally and spatially into the new facility. This request, and the overall scale and building configuration presented some unique design challenges.