Stage 1: Proposal and Process Development
Stage 2: Process Design Package
Stage 3: Detailed Engineering and Construction
Stage 4: Shipping and Installation
Stage 5: Commissioning, Start-up, and Performance Test
Read a more detailed list on the Advantages of Modular Construction here
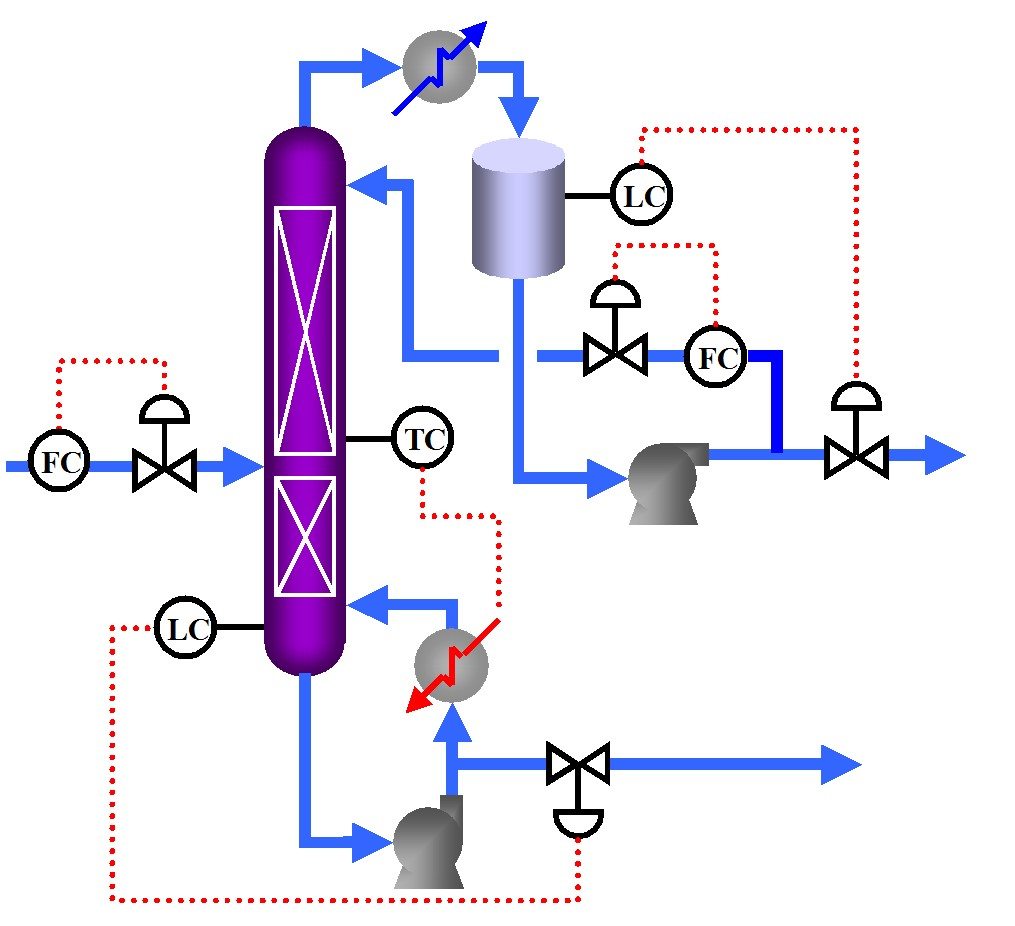
Proposal and Process Development
The first stage of the project starts with a customer inquiry and focuses on process development. Koch Modular will work collaboratively with the client to develop the process design basis and define the overall scope. The objectives of this stage will be to establish plant capacity, product recovery, and purity requirements, and identify appropriate project specifications. Koch Modular utilizes a “checklist” approach via a comprehensive inquiry form to thoroughly extract all the information necessary to develop a design and scope of supply that will meet project requirements and can be provided with a Process Performance Guarantee.
Chemical Process Engineering – Concept to Conceptualization
With the design basis established, Koch Modular begins the process of design conceptualization and develops an accurate model of the mass transfer system:
- Selection of Equilibrium Data and Activity Coefficients
- Development and Optimization of Chemical Process Simulations
- Identify the need, if any, for pilot testing
Based upon the process simulation, unit operations are selected and a process flow scheme is developed. Reliability, redundancy, flexibility, and cost optimization are considered.
- Process Flow Diagrams (PFD’s)
- Preliminary Piping & Instrumentation Diagrams (P&ID’s) for cost estimating
- Preliminary Equipment list / sizes
Koch Modular piping designers develop a three dimensional equipment layout.
- Footprint and modular layout of overall system.
- Accessibility and optimization in consideration of the available plant space.
Koch Modular will then provide a detailed proposal for the design and supply of a modular system that meets process requirements and project specifications.
- OOM (Order of Magnitude), Budgetary (+/- 20%) or Fixed Price depending on client needs and current accuracy of scope/design basis
- Includes design basis summary, utility consumption, equipment list, module footprint(s), division of responsibility, schedule and many other details
- Includes details of Koch Modular Process Performance Guarantee
Process Design Package
Once the Process Development Stage is complete, its product, a well-defined process design basis and conceptual design, will serve as the foundation for the development of the Process Design Package. During this stage, Koch Modular works closely with the customer’s project team and shares their experiential insights to identify opportunities for cost savings, schedule reduction, and design efficiency.
The Process Design Package is a front end engineering package that defines the entire scope of supply via drawings and specifications.
- Process Flow Diagrams (PFD’s)
- Piping & Instrumentation Diagrams (P&ID’s)
- Heat Exchanger thermal designs
- Mechanical drawing lead sheets for columns, vessels, and heat exchangers
- Pump hydraulic calculations and specification sheets
- 3D equipment general arrangement drawings
- Participation in a HAZOP review meeting
- Detailed Project Kick Off List, defining all project scope of supply requirements
- Client review, comment, and approval process
Our Process Design Packages undergo a comprehensive internal and external review process and include all of the necessary drawings, specifications, calculations, selections and support documentation required to assure our clients that the process design will meet their project requirements. Best of all, our proposed process designs come with Process Performance Guarantees.
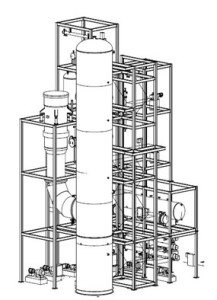
Detailed Engineering and Construction
Through our diverse engineering expertise, Koch Modular engineers and designers are able to completely and systematically define each component of a modular process system. Equipment, piping, structural steel, instrumentation, electrical and controls systems are all evaluated, optimized, and detailed for fabrication. Our senior project managers oversee and orchestrate the overlap and interaction of the multiple engineering disciplines and vendors required to successfully and efficiently execute our customers’ projects.
Detailed design, procurement, and fabrication are executed in parallel which allows for overall project schedule compression.
During detailed engineering, Koch Modular provides the client with all the information necessary to prepare the job site for delivery, obtain permits and streamline the installation process. These items include foundation loads, anchor bolt patterns, piping tie-in coordinates, electrical drawings, PSV calculations and emissions summary, modular lifting plan, shipped loose items, and a comprehensive installation manual.
The 3D piping model allows for a series of model reviews, where the client can take a virtual walk-through of the modules before fabrication begins, helping with the approvals that affect the operation, maintenance, and access requirements.
After process equipment is fabricated and inspected, it is all shipped to the module assembly shop along with other procured components such as instrumentation and manual valves. The module assembly shop installs all equipment into structural steel frames. After the equipment is mounted in the steel structures, all point to point process and utility piping is installed. Instruments are wired to remote I/O control panels mounted on the first floor of each module. The modules are complete with ladder or stair tower access, lighting, a process control system (if desired), equipment and piping insulation, safety showers and eye wash stations, a fire suppression system, utility stations and convenience receptacles.
The final activity in this phase is a customer-witnessed final inspection and Factory Acceptance Test (FAT) performed at the module assembly shop.
Shipping and Installation
Modular process systems engineered by Koch Modular are specially designed for transport by road, rail, water, or air, and arrive ready to install. Koch Modular has extensive experience and vendor relationships with freight forwarders to safely and efficiently ship systems of various shapes and sizes to locations worldwide.
Process modules are staged to arrive at the plant in sequential order. Once modules are set on foundations, they are anchored for stability. The remaining installation effort includes installing any shipped-loose items and completing process and utility piping tie-ins, and necessary electrical connections.
Koch Modular provides a lifting plan and comprehensive installation manual to support the installation process. Our customer’s typically use a local Engineering, Procurement and Construction Company to install the Koch Modular modules and to provide the balance of plant scope of supply which includes foundations, utility generation and distribution, storage tanks, pipe racks, motor control center, etc.
Koch Modular engineers are available to provide on-site installation support, as required by our customers.
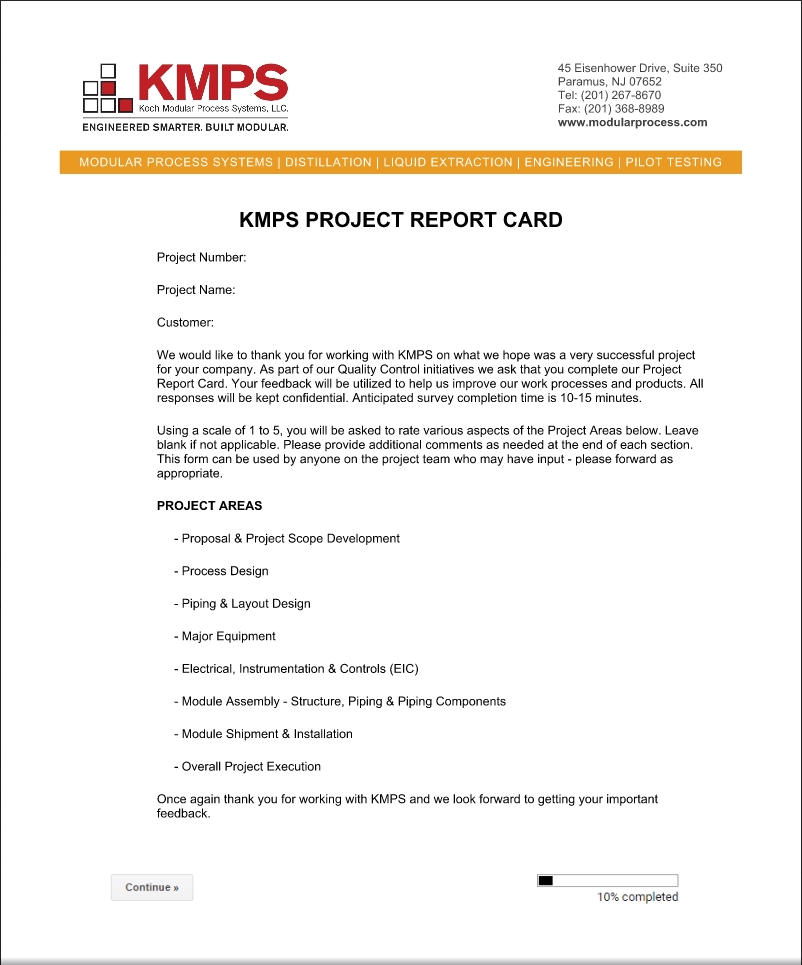
Commissioning, Start-up, and Performance Test
Once the modules are installed, commissioning and functional testing is performed to ensure there are no leaks in the system and everything is in working order. Control valves are cycled, instruments and the control system are checked, and pump operation is verified, just to name a few of the activities performed. Koch Modular supplies a complete checklist of commissioning activities in the installation and operating manual.
Continuing project support is extended to all customers after module shipment to participate in commissioning, start-up, troubleshooting, operator training, or validation.
Koch Modular operating manuals contain all the information needed for successful commissioning, startup, shutdown, and troubleshooting of the modular process system.
- Performance & Design Basis
- Process Operation, Description, and Control Philosophy
- Commissioning: Instrument & Equipment Checkout
- Hydraulic Start-up and Test Procedure
- Process Startup & Shutdown Instructions
- Quality Control & Troubleshooting
- Reference List of Alarms and Interlocks
- Suggested Tuning Constants