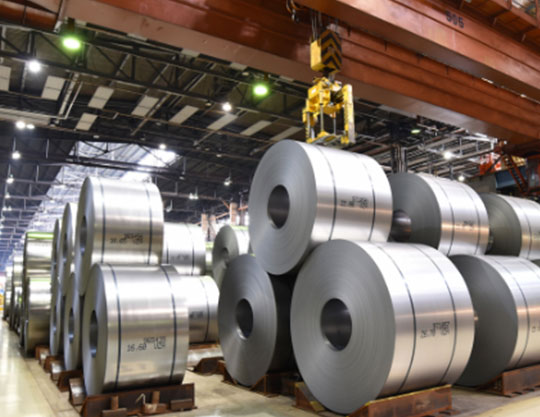
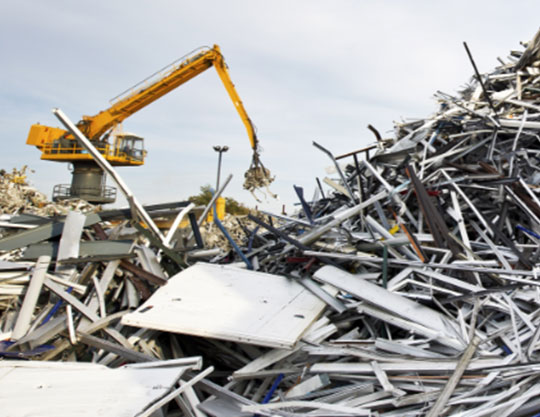
Recently, there has been a greater push towards recovery of metals from waste materials, particularly from electronic waste. Solvent extraction (SX) is well established within the hydrometallurgical industry, generally starting with mining operations, as a means to recover these metals. A key aspect of any type of metals purification via SX is the selection of the appropriate solvent system for the metal components in question. These solvents typically consist of an extractant for the specific metal, a diluent to facilitate mass transfer, and, sometimes, a modifier to alter physical characteristics.
Once the optimal solvent is selected for the metals extraction process, equipment must be designed for the commercial installation. Multistage, continuous mixer-settlers have been the workhorse for many metal recovery processes used in mining operations, although agitated extraction columns are sometimes used in these processes. Agitated extraction columns offer significant advantages for metals recycling processes which tend to be smaller in scale than large, industrial mining processes. These advantages include considerably smaller footprints and significantly reduced solvent inventories as well as improved efficiency.
With Koch Modular’s chemical separations and mass transfer expertise, particularly in the area of SX technology, and historical involvement in novel technological solutions in the field of advanced recycling, is well poised to contribute to the design of commercial liquid-liquid extraction equipment for the metals recovery/recycling industry. Koch Modular offers a number of different types of agitated extraction columns including KARR ® and SCHEIBEL® Columns. This allows Koch Modular to select the appropriate extraction technology for each individual application. In addition, the push to decentralize production, and thereby de-risk supply chains, is addressed via Koch Modular’s modularization expertise. Our modular design capabilities make it possible to locate processing plants near waste collection or generation sites.
Koch Modular’s experience extends to the extraction of the following metals from pregnant leach solution, derived from mining operations, electronic waste and spent battery liquid among others:
- Industrial metals – copper, aluminum, steel, zinc, precious metal palladium
Koch Modular supports the metal recycling industry with:
- Replacing traditional mixer-settlers with more efficient agitated extraction columns.
- Solvent selection through liquid-liquid equilibrium data development
- Advanced process design capabilities
- Pilot testing of new separation processes
- Proprietary extraction technology (KARR® and SCHEIBEL®)
- Reduced Footprint
- Minimized Solvent inventory
Simplified Flow Diagram for Typical Recovery Process (3-column system)
SX processes for recovery and purification of metals typically involve three process steps:
- Extraction – selective extraction of the targeted metal. The acidic raffinate is often recycled back to a metal digestive step.
- Scrubbing – removal of co-extracted contaminants from the loaded organic leaving the extraction column using a selected “scrub solution”.
- Stripping – extraction of the targeted metal from the loaded organic using an aqueous “strip solution”. The purified metal leaves with the spent strip solution and the organic phase is recycled back
Koch Modular provides clients with the development, design and supply of these extraction columns and processes, offering to provide them in a complete modular system with a process performance guarantee. Developing the process is a key element to the optimal design for these systems. Koch Modular offers the ability to test all SX steps in pilot scale extraction columns. Jacketed, glass KARR® and SCHEIBEL® columns can be tested in our pilot plant facility, or the columns can be supplied on a sale or rental basis for on-site testing at the client’s specified location. Once successful testing has been completed in our pilot columns, scale up data is generated that is used to offer the commercial design with a process performance guarantee.
Case Study
A client was using a 3-stage mixer/settler system to extract and recover a valuable metal from recycle filaments. This equipment had experienced long-term corrosion and required replacement. The filaments were first digested in a strong acid solution and then extracted using a solvent consisting of a tertiary amine extractant in an aromatic diluent. Looking for more efficient extraction equipment, the process was successfully tested in a 3” diameter pilot SCHEIBEL® Column. Based upon the results from the testing, a commercial SCHEIBEL® Column was designed and supplied, effectively replacing the mixer-settler. This column has been providing excellent metal recovery of more than 10 years.
Our Extraction Technology Experts
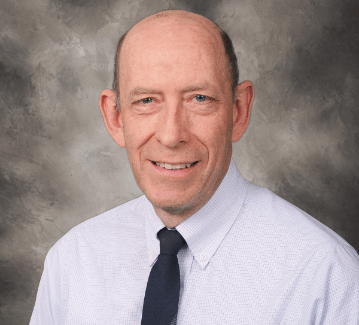
Don Glatz
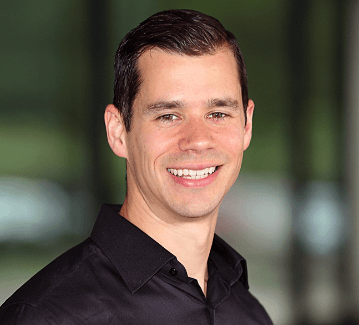