Building with Confidence: Behind the Scenes of Modular Assembly
December 2024
/Category:Modularization
James Boklage, Quality Assurance and Quality Control (QA/QC) Manager at Koch Modular, is immersed in the final stages of preparing an 80,000-pound modular processing system for delivery—saving the client time, money, and the inevitable headaches of on-site construction.
“One of the biggest positives about modular assembly is being able to fabricate something off-site,” Boklage explains, gesturing to the fully assembled module behind him. "When it’s under a roof, that’s the best scenario for us because we don’t get shut down for inclement weather. That helps us maintain our schedules quite a bit."
The process isn’t just about efficiency; safety and quality are also paramount. Currently horizontal in the fabrication shop, the module will be erected vertically once it arrives at the client’s site. “By keeping it horizontal, we are keeping everyone closer to the ground, so that’s inherently a lot safer situation,” Boklage says, highlighting the proactive approach to worker safety.
Ensuring quality across each component is a sophisticated operation, as Koch Modular sources parts from vendors across the country and even globally. “The quality assurance department is setting the standards of the quality of products that we’re getting from our vendors,” he explains, noting the extensive inspection and testing protocols that vendors must meet. Koch Modular’s quality control inspectors closely monitor these standards, ensuring that each component meets the company's rigorous requirements.
Various personnel within Koch Modular help to perform an essential role in ensuring the success of each modular assembly by performing a comprehensive 13-step walk-down to guarantee quality, safety, and readiness. This walkdown team typically includes personnel from the Project, Process, Piping, and QA/QC departments. This structured process keeps each day dynamic and engaging as the team checks each critical aspect of the module before it leaves for the client site. Starting with inventory checks, they verify that all structural steel is correctly oriented and securely bolted, meeting torque specifications to uphold integrity. They also check grating, equipment installations, P&ID accuracy, piping isometrics, pipe tracings, and insulation, among other things. “We’re performing isometric walk downs to make sure all the valves are turned in the right direction, making sure that instruments are facing the right way,” Boklage says.
The process also includes a rigorous factory acceptance test (FAT) where the EI&C team tests every instrument and control valve to confirm effective communication with their designated equipment. This step is crucial for minimizing the risk of onsite surprises and enables a smoother setup for the client. Finally, as part of shipping preparation, the Project Management and Quality Control team members inspect the entire module, checking for any loose components and ensuring each piece of equipment is securely strapped down for safe transit. Temporary supports are added where necessary, providing additional stability for transportation.
“It makes me proud to say I work with Koch Modular,” Boklage reflects with a smile. I feel safe working here in this environment, and I like working for the company.” As the module is readied for its journey, it’s clear that pride, precision, and quality assurance are embedded in every step of the process, from concept to commercialization. At Koch Modular, the promise of reliability and efficiency isn’t just a goal—it’s a standard.
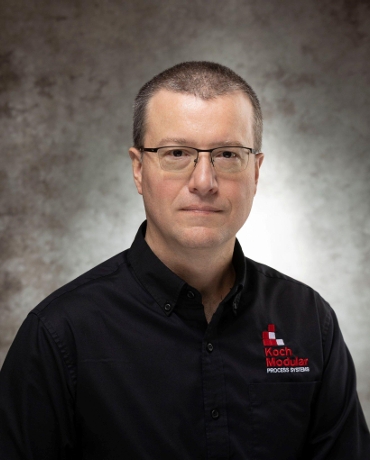
Meet James
James is a licensed Professional Engineer (PE) in Pennsylvania and Kentucky, with a Master's degree in Mechanical Engineering. His primary focus has been pressure vessel design and inspection. His career spans over 25 years, with experience in the following industries: static equipment design and fabrication, petrochemical and chemical plants, fossil and nuclear plants, and mechanical and nondestructive testing.
James is currently the Mechanical Engineering, Quality Assurance, and Quality Control Manager for Koch Modular Process Systems, where he has worked for over 15 years.
James Boklage PE, Koch Modular Mechanical Engineering Manager, Quality Assurance and Quality Control (QA/QC) Manager